Since the invention of the recovery boiler in the 1930s, energy and water usage in pulp and paper mills has been highly integrated. This high level of integration helps keep mills running efficiently, but it can also create challenges as mills increase production yet try to reduce energy and water usage to conserve resources and prevent incremental production costs from rising. This means there is a lot to consider to ensure that modifying consumption in one area will not be offset by increased consumption or different production inefficiencies elsewhere. This post provides an overview of how the engineers at Allnorth use proven tools and processes to evaluate energy and water usage in mills and then develop the most appropriate holistic long-term and sustainable energy and water efficiency solutions.
Invest Capital Wisely by Understanding Your Mills’ Incremental Economics
In the pulp and paper industry, capital for improvements can be difficult to come by. When funds do become available for mill optimization efforts, you need to be sure you are focusing on projects that will result in an excellent return on investment (ROI). Therefore, before starting any mill optimization efforts, it is first important to understand the incremental economics of your production. As with any production process, as you push the facility more, you will reach a point where equipment will operate less efficiently and the cost of the fiber and fuel to produce each incremental ton will increase. Thus, to increase production and prevent incremental costs from rising as well, it makes sense for mills to look for ways to optimize water and energy consumption.
Understanding the Intricacies of Your Mill with a Process Integration Approach
Due to the highly integrated nature of processes within pulp and paper mills, when looking to reduce the incremental cost of increasing production by optimizing energy and water usage, individual system or process improvements cannot be examined in silos. As shown in Figure 1, unit operations of the mill are interconnected and depend on energy and water resources passing through from one area to the next.
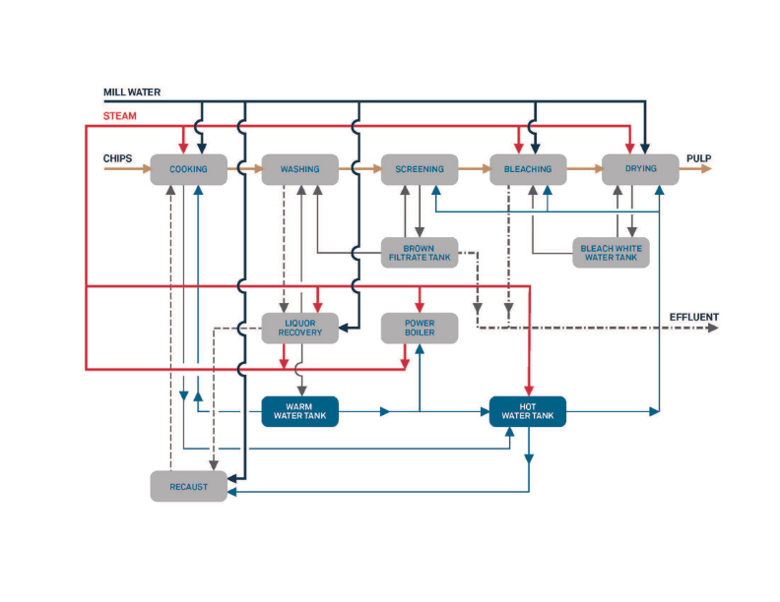
Figure 1. This diagram shows how energy and water are transferred and/or reused between various equipment and processes within a mill.
Therefore, it is critical to take a process integration approach when identifying areas of the mill for potential efficiency gains. With a process integration approach, it is possible to look at the entire complex as a whole, identify interactions between different equipment or steps in the process, and then determine the best way to use resources effectively while reducing costs. Since there are many complex interactions in the mill, this is not a simple task. But at Allnorth, we can draw on both the many years of direct industry experience our engineers have working in mills, as well as our proven modeling experience and expertise with software such as CADSIM Plus to create mass and energy balance models for visualizing solutions.
Through this approach, we can eliminate unforeseen problems such as reducing energy usage in one area yet increasing the energy needed in another area because the two processes depend on each other. In short, this model-based process integration approach offers significantly improved certainty that you can achieve your desired benefits and ROI when engaging in an energy and water optimization initiative before you invest in expensive equipment.
A Practical Example: Developing a Holistic Solution with a Model-Based Process Integration Approach
As a mill increases production, area operations often get out of balance. This means machines will run at higher loadings than they were designed for, and inefficiencies such as needing more water to wash chemicals from pulp or heat exchanger constraints will start to pop up. To help mills get their efficiencies back in line and reduce conversion costs, a holistic approach to reviewing capacity constraints and developing solutions to optimize energy and water usage for elevated production rates is necessary.
To do this, we begin our optimization engagements by meeting with a cross-functional team of mill operation, technical, and maintenance personnel to gain insight into the mill’s current constraints and operational inefficiencies. While each mill is different, our team of process experts can still leverage their collective experience to understand how the mill’s current inefficiencies can be addressed. This approach is more productive for truly understanding how process targets can have an impact on down or upstream areas and is superior to having one-on-one discussions with individual process owners.
After we better understand a mill’s processes and their objectives, we recommend conducting a feasibility study. This study should define the mill’s current base case operation and then incorporate the development of computerized models to accurately demonstrate the impact of process or energy modification on the mill as a whole. For example, we recently worked with a mill that was putting an abundance of warm and hot water into its sewer system. This was creating multiple inefficiencies as energy was being lost down the drain, and in the summer months, cold water had to be added to the sewers to keep the water going into the wastewater treatment plant below 40°C.
Figure 2. An example of part of a water treatment facility within a pulp and paper mill.
To remove these inefficiencies, we holistically looked at the mill to identify areas for improvement. We started this process by creating separate high-fidelity models for winter and summer operations for the mill’s thermal, power, and water systems using CADSIM software. As a result of our feasibility study and process models, we identified multiple areas with high confidence where the mill could reduce steam and water consumption.
A Proven Approach to Optimizing Pulp and Paper Production
By using the proven process integration and modeling approach described here and drawing on the experience of our in-house certified energy managers and engineers who have spent many years working in mills themselves, we help mills achieve their energy reduction goals and sustain them. This may mean identifying opportunities for either repurposing resources or areas where energy and water consumption can be reduced. Oftentimes we even determine there are inexpensive retrofits that can result in payback periods of just six months to a year. Whatever the best option is, we can then develop scalable solutions that will benefit the entire mill by offering increased reliability and avoiding production losses.
Download our latest white paper, Addressing Resource Consumption Inefficiencies In Pulp and Paper Production, to learn more about our proven approach to optimizing energy and water usage in the pulp and paper industry.
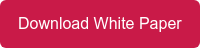